A robust business model prioritizing quality at every step of the process is central to any successful medical device company. History has shown that a critical point of failure in many medical device companies is when quality is not at the forefront of product design, R&D development, go-to-market and sales.
Today, most at-home lab tests you see on the store shelf or e-commerce sites for diabetes, cancer, STDs/ STIs, food sensitivities, metabolism, thyroid, testosterone, cholesterol, and others are laboratory-developed tests, otherwise known as LDTs. Recent potential rulemaking from the FDA has brought LDTs into focus across the regulatory industry.
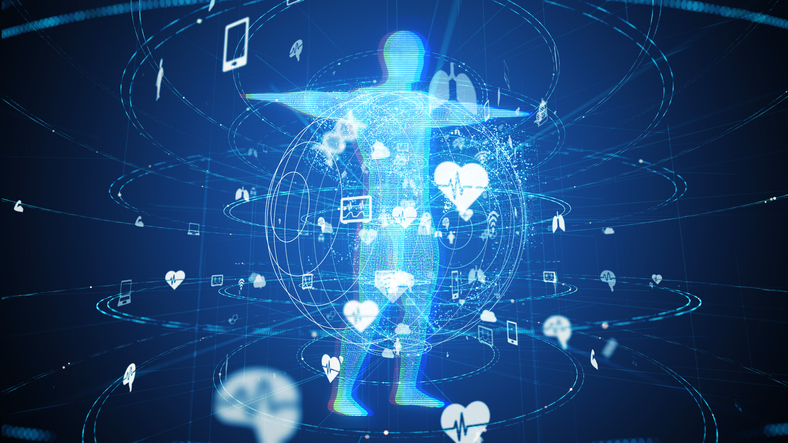
With the Rise of AI, What IP Disputes in Healthcare Are Likely to Emerge?
Munck Wilson Mandala Partner Greg Howison shared his perspective on some of the legal ramifications around AI, IP, connected devices and the data they generate, in response to emailed questions.
There is speculation to date that LDTs that currently require Clinical Laboratory Improvement Amendments (CLIA) certification will be required to pass the more stringent ISO13485 audit . CLIA regulates all laboratory testing (except research) performed on humans in the U.S. Currently, the Centers for Medicare & Medicaid Services (CMS) is the regulatory body that oversees CLIA certification. [Although all clinical laboratories must be properly certified to receive Medicare or Medicaid payments, CLIA has no direct Medicare or Medicaid program responsibilities.] In 2022, there was proposed legislation, that ultimately did not get passed. However, in 2023 we should expect to see new proposed rulemaking and focus on LDT regulation.
In my 30+ years in the therapeutic and diagnostic device quality space, there is one constant that I have come to understand. Success in the medical device industry comes down to quality.
Here are 3 top things you can do at your organization to ensure quality is top of mind when developing at-home diagnostics:
- Strong documentation – When a medical device company designs and engineers for reliability, it includes strong documentation that becomes the basis of the future Quality Management System (QMS). Laboratory or production line feedback from the people running the test or building the device is an often-overlooked step until audit prep. These boots on the ground have valuable information and suggestions for improvements. Record everything and don’t overlook the people working with the test/product daily. If everyone starts with the expectation of recording the good and the bad, a medical device will constantly improve, problems will be spotted before they become catastrophes and the laboratory or manufacturing component of the QMS will be easier to formalize. Ask yourself the question: How will you know if standards are being met if the standard has not yet been established and/or baseline?
- Extend quality to your suppliers – The supplier’s quality affects your quality. Make certain they know quality and consistency are important to you. Your purchasing department needs to manage your suppliers with quality in mind. It is their responsibility, not the quality department, to record issues for future reference. This is the basis of the supplier management component of the QMS.
- Sound customer relations and post-production monitoring – Customer relations and post-production monitoring is another important aspect to the ground-up quality model. Whoever in your organization receives the customer feedback or complaints should document it according to the QMS and notify Operation, Regulatory, Quality and whoever else in your organization that is responsible for your medical device business meeting certain standards.
Ensuring Quality is the best first step any company, especially startups, can take steps toward preparing for future changes to LDT regulations. Hire and lean on your quality expert to formalize documents to meet requirements, find gaps in best practices, and utilize internal audits to verify standards are being followed. The reality is that every employee has an important role to play and is ultimately responsible for quality.
Photo: marchmeena29, Getty Images
Michael Gomez is an experienced Quality Executive with thirty years of medical device experience in Therapeutics and Diagnostics including LDT’s. Prior to joining Simple HealthKit, Gomez was Head/Sr. Director of Global Quality Assurance at Predicine where he implemented and maintained the company’s global Quality Management System. He also held Senior Quality Executive positions at CareDX, Ripple LLC, and ArcherDX and is skilled in writing, implementing, and maintaining complete quality management systems compliant to ISO 13485 (EU QMS), title 21 CFR 820 (FDA QSR) and title 42 CFR 493.1200-1299 (CLIA Lab QMS).